事例紹介
製造現場の見える化で、製品不良率の改善と収益回復
POINT
【三井屋工業株式会社】
・電子日報アプリの入力で、月600枚の紙をデジタル化
・生産実績情報をリアルタイムで管理・問題の早期発見で不良率を4.0%から0.4%に改善
・労働環境の改善で、離職率は約10%から1.6%へと激減
取組イメージ
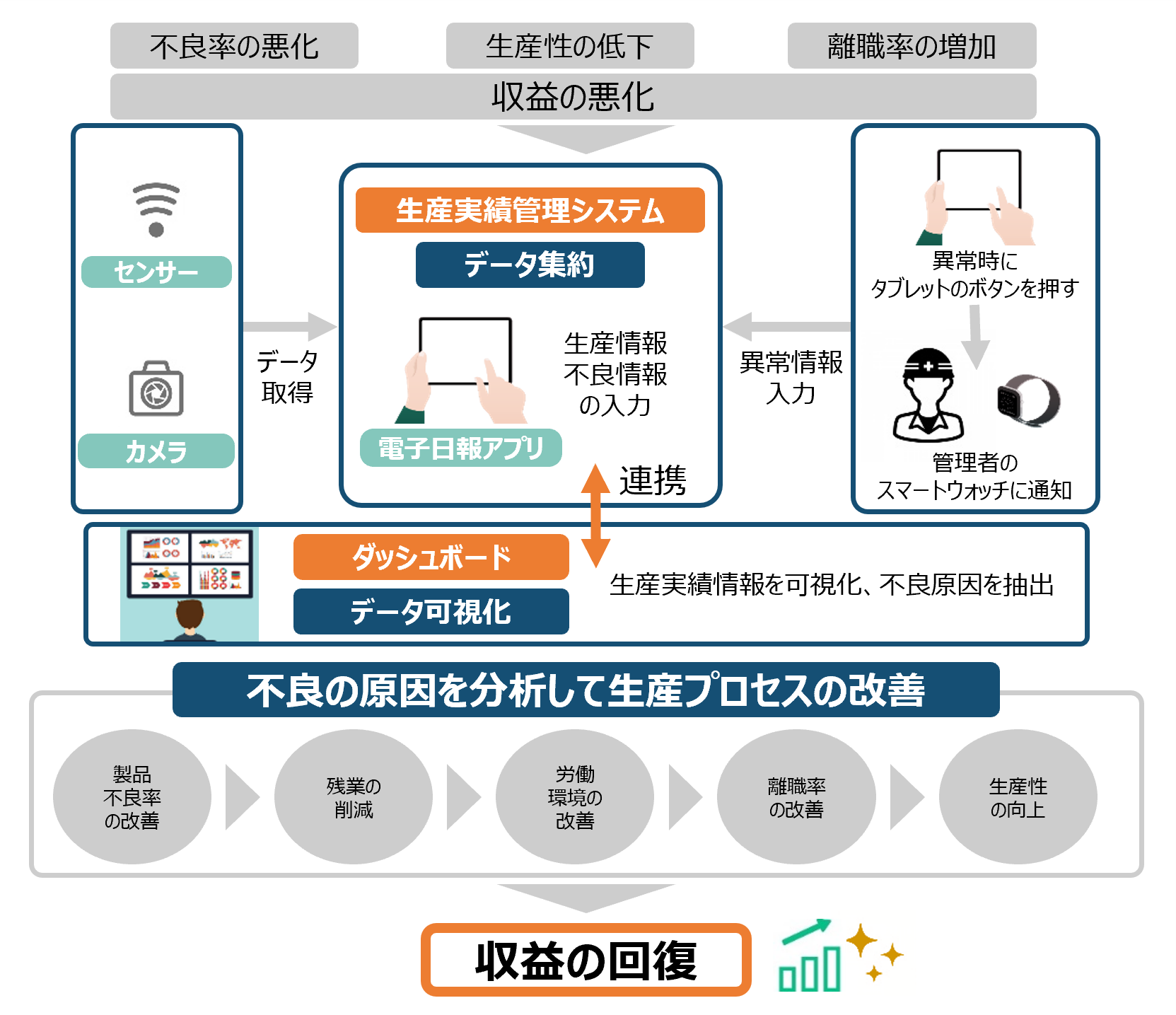
課題内容
〇自動車用の内外装部品を製造しているが、不良品が多いことによるコスト増加や製品不良率を改善するための残業増加で、収益悪化の課題を抱えていた。
・紙ベースで上がってきた不良率が2%程度なのに、財務データによる実際の不良率は4%以上であり、正確な製品不良率を管理・把握できていなかった。
・紙の日報を用いて作業工程管理を行う中で様々な問題を抱えていた。
(集計ミス・書き漏れ・書き間違い・他国籍の従業員が書いた言語が読めないなど)
・会社の経営状態に不安を感じた従業員が離職し、現場の生産性低下、不良率がさらに悪化するという状態になった。
実施概要
〇製造現場を客観的・定量的に把握するため、ソースコードをほとんど使わずにシステム開発できるローコードツールに着目し、日報を電子化して現場状況の見える化を行った。
〇電子日報アプリの日報やセンサー、カメラから取得できたデータ(生産情報、不良情報など)を生産実績管理システムに集約し、集約情報を基に稼働状況・ロスの要因分析を「工程別・品番別・作業者別」の項目で確認し、改善の優先順位付けを行った。
〇生産実績管理システムで集約した情報を、生産進捗の可視化のためダッシュボードと連携し、計画の進捗状況を関係者間で共有した。
〇異常時に作業者がタブレット上のボタンを押すことで、管理者のスマートウォッチに異常発生の連絡が届き、その情報を生産実績管理システムに入力し、データとの紐づけを行うことで、迅速な対応が可能になった。
効 果
〇月600枚の紙をデジタル化。日報の集計は自動化され、転記ミスがなくなった。
〇現場では生産情報や不良情報が集約され、生産状況を管理できるようになり、異常があれば早期発見、対応することができるようになった。不良率は4.0%から0.4%へ改善した。不良の原因が分析できるようになったことで、改善・再発の防止に繋がった。
〇不良率を改善するために残業が発生していたが、労働環境が改善され、離職率は約10%から1.6%へと激減し、収益が回復した。
〇現場のデータを見える化したことで、従業員に新たな気づきが生まれた。労働環境の改善に伴い従業員間のコミュニケーションが増加したこともあり、その気づきを従業員間で共有し、モチベーションの向上にも結び付いた。
ITツール
使用ツール | HiConnex > |
---|---|
取り扱い企業 | セレンディップ・ホールディングズ株式会社 > |
ツール概要 | 作業日報を電子化、KPIの把握、生産実績をベースとした管理が可能 |
使用ツール | MotionBoard > |
---|---|
取り扱い企業 | ウイングアーク1st株式会社 > |
ツール概要 | データを集約・可視化、データ活用に必要な機能を1つのプラットフォームで提供するツール |
補助金活用
IT導入補助金
課題分類
生産プロセスの改善
社内の働き方改革
人手の確保・育成
DX実践の目的
サプライチェーン
参照:経済産業省. “DX Selection2023(P17~18)”. https://www.meti.go.jp/policy/it_policy/investment/dx-selection/dxselection2023report.pdf, (参照 2023-11-1)
参照:ウイングアーク1st株式会社. “導入事例・三井屋工業株式会社 | 導入事例|ウイングアーク1st”. https://www.wingarc.com/product/usecase/904.html, (参照 2023-11-1)