事例紹介
自社開発の生産管理システムで最新情報の共有と新ビジネスの創出を実現
POINT
【日本ツクリダス株式会社】
・誰でもいつでもシステム上で最新情報(製造・加工の進捗、出荷状況など)を取得でき、工程の最適化が図れ、作業効率が上がった
→完全週休2日制を実現
→事務仕事が削減され、人件費が半分に(事務職員2人→1人)
・システム販売というストックビジネスを会社の新しい事業の柱として展開(システム導入企業162社)
取組イメージ
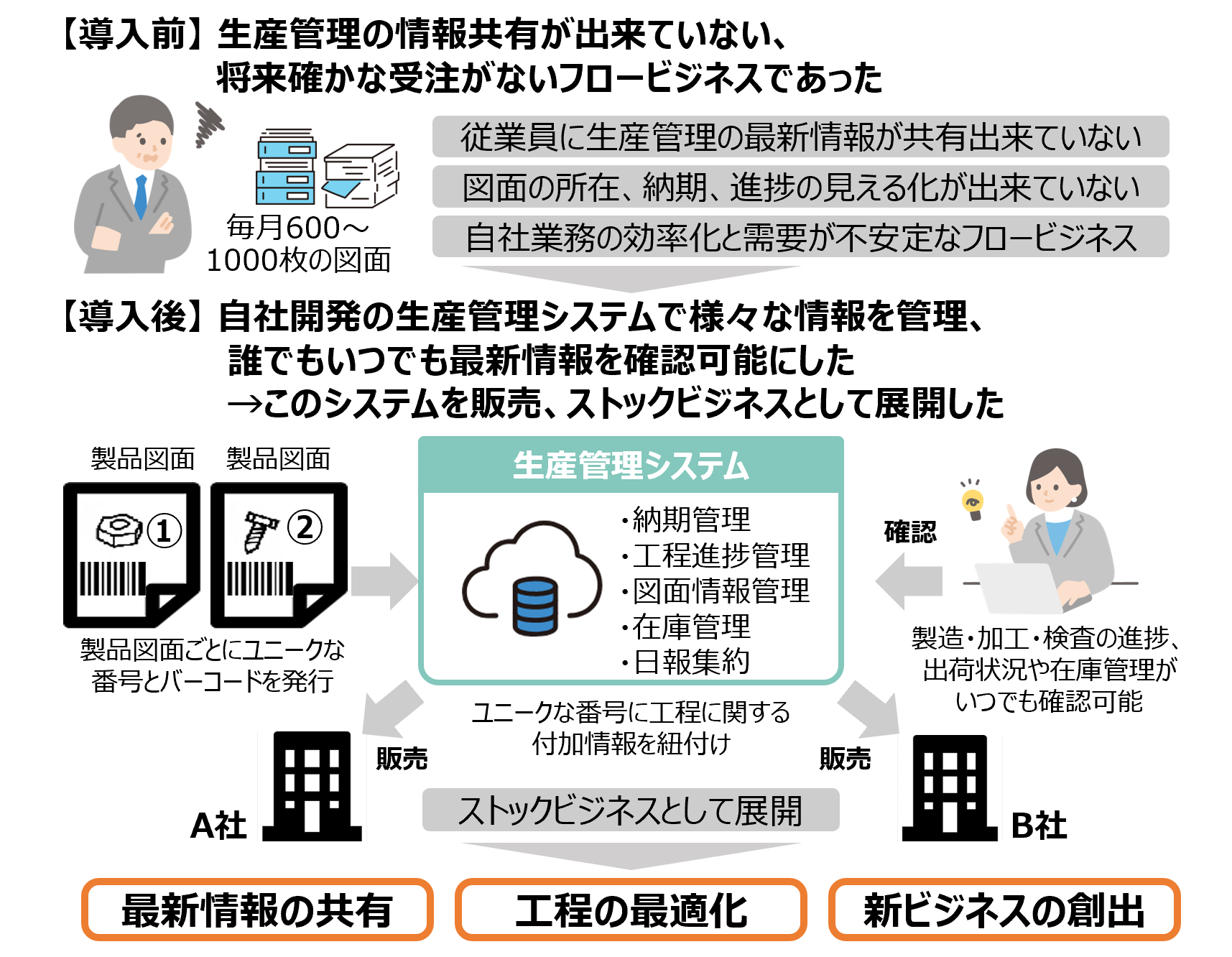
課題内容
〇金属加工業をメインに事業展開しているが、金属加工の現場において生産管理の情報共有が出来ていない、将来確かな受注がないフロービジネスであるといった課題があった。
・現場において納期や進捗などの生産管理は社長や工場長の頭の中で行われることが多く、従業員に最新情報を共有することが出来ていなかった。
・多品種少量生産のため、1ヶ月で600~1000枚に及ぶ図面に対し、図面がどこにあるか、納期はいつなのか、どこまで進んでいるのか等の管理が困難となっていた。
・金属加工業は、将来的に確かな受注があるのかが見えないフロービジネスであり、自社の業務を効率化したいという思いと、安定した需要のあるストックビジネスを立ち上げたいという思いがあった。
実施概要
〇図面1枚毎の工程管理にフォーカスし、納期管理や工程進捗管理、図面情報管理、在庫管理、日報集約などがまとめて行える生産管理システムを自社で開発、運用した。
〇1枚の図面に対してユニークな番号とそのバーコードを発行し、その番号にすべての工程に関する情報を紐付け、登録・管理・確認ができるようにした。
〇社内や外注先の製造・加工・検査の進捗、出荷状況、在庫管理など、1枚の図面のあらゆる情報をシステム上で一元管理し、誰でもいつでも確認できるようにした。
〇「同じ悩みをもつ製造現場で必ず需要があるはずだ」と考え、このシステムを販売し、ストックビジネスとして展開した。
効 果
〇1つの案件ごとの状況が可視化され、各工程で部分最適が行われた。また、全部門の担当者がシステム上で各案件の最新情報を確認できるため、各工程の担当者が全体の工程を見渡し、前工程に対して要望を言ったり、工程の全体最適も行われた。
〇各工程の担当者は指示がなくても自分がやるべきことが分かり、工程が変わる際の指示も必要なくなり、全体の流れが早くなるなど作業が効率化されたことで、売上を下げないまま完全週休2日制を実現できた。
〇誰もが常に最新の情報を共有・把握できるようになり、事務仕事(案件の全体把握など)が削減され、人件費が半分になった(事務職員2人→1人)。
〇生産管理システムの導入企業が162社となり、ストックビジネスとして会社の事業の柱となった。
苦労点
デジタルツールが苦手だという従業員もいたが、会社の方針を全て共有したり、社長自ら率先して動くことで協力的な雰囲気が生まれた。また、デジタルを使う方が便利だという成功体験を重ねることで、使うのが当たり前、変化に抵抗のない組織文化を育てた。
ITツール
使用ツール | エムネットくらうど > |
---|---|
取り扱い企業 | 日本ツクリダス株式会社 > |
ツール概要 | 納期管理や工程進捗管理、日報の収集などができる生産管理システム |
補助金活用
課題分類
新しい事業・サービスの創出
生産プロセスの改善
ビジネスモデルの変革
DX実践の目的
コミュニケーション